Importance of use of super clean fluid in the Hydraulic System
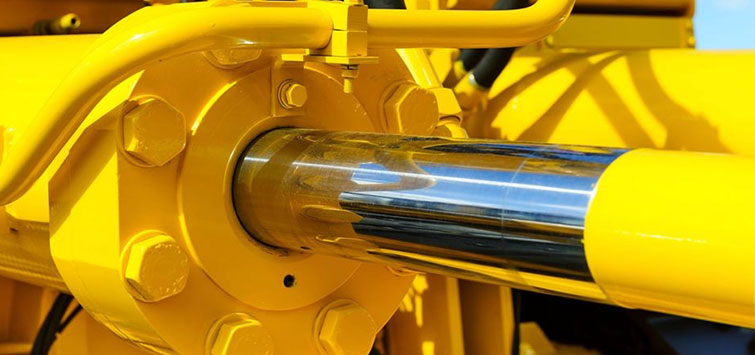
Introduction
A hydraulic power unit is an arrangement of components, which is used to control hydraulic energy. Mainly comprised of a motor, pump and reservoir. Hydraulic systems are used in any form of mechanical device to push, pull or lift. The primary components required to achieve this are discussed below.
- Motor -AC or DC or Internal combustion engine
- Hydraulic Pump - Common types gear, piston or vane
- Reservoir - Holding tank for hydraulic media
- Filtration - Commonly a strainer for pump inlet, pressure filter for pump outlet, and/or return line filter
-Filtration is a critical part of hydraulic power units, _ ensuring wear is minimised and efficiencies are maintained.
-Suction strainers capture the largest of contaminants and ensure they do not enter the pump. Pressure filters are selected when highly filtered oil is required within the hydraulic system. Contamination within the system is filtered out by the return line filter before it enters the hydraulic reservoir.
-Filterability of a hydraulic oil is significantly influenced by the additives used in the formulation and by the overall hydrolytic stability of the oil
- Control Valves - There are many different types of control valves used in many different ways. Pressure control valves limit or control the hydraulic pressure within the hydraulic system. Directional control valves direct the flow of oil around the system and are controlled manually, electrically, hydraulically or pneumatically. These valves are used in separately or combination to gain the desired function of actuators, motors and other components.
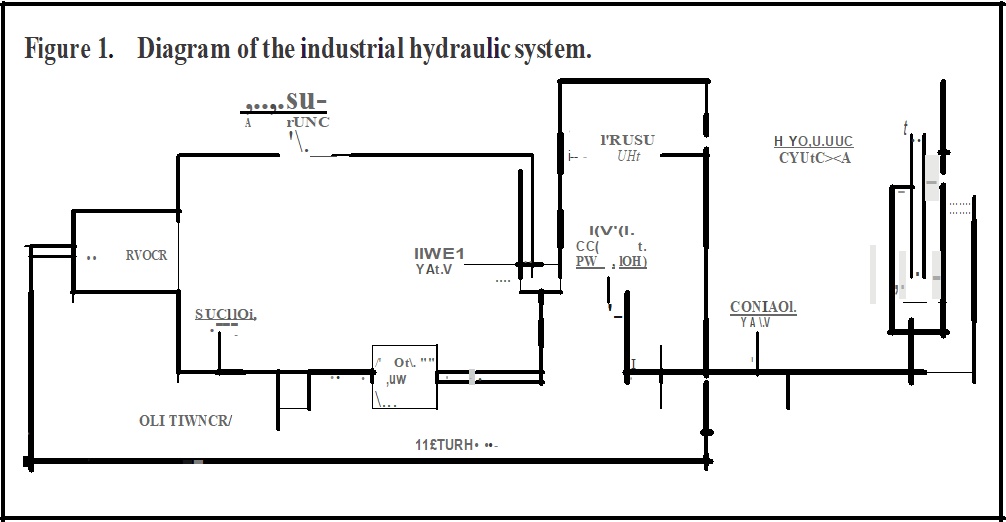
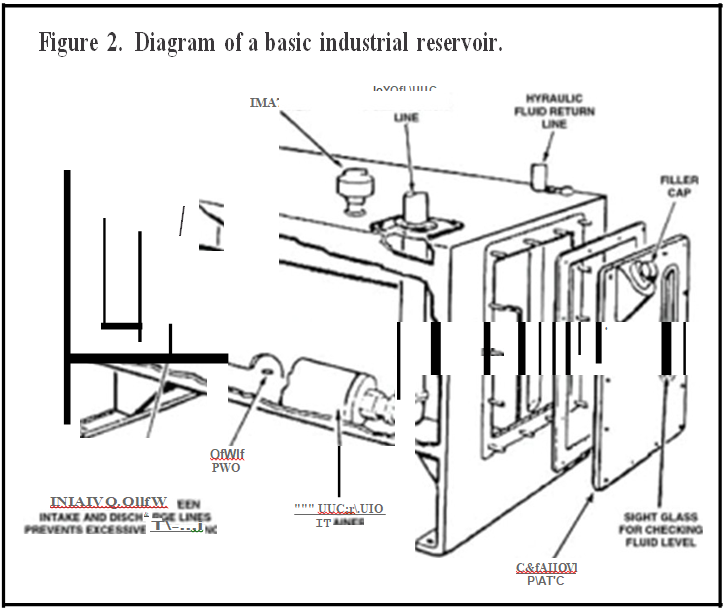
Modern day applications of hydraulic power units are extremely diverse and divided into mobile applications· (agricultural machinery, diggers, graders, road maintenance vehicles, forklifts, excavators, etc.), industrial applications (machine tools, food processing machinery, automatic handling and assembling equipment, steel works and mining, etc.), and other applications (automotive, aerospace, marine, medical.)
Contamination Cause & Effect:
The main cause of hydraulic system failure has been high: level of contaminants found both in fluid and system in existence. In spite of taking all precautions there is always a chance of contaminants getting into the system.
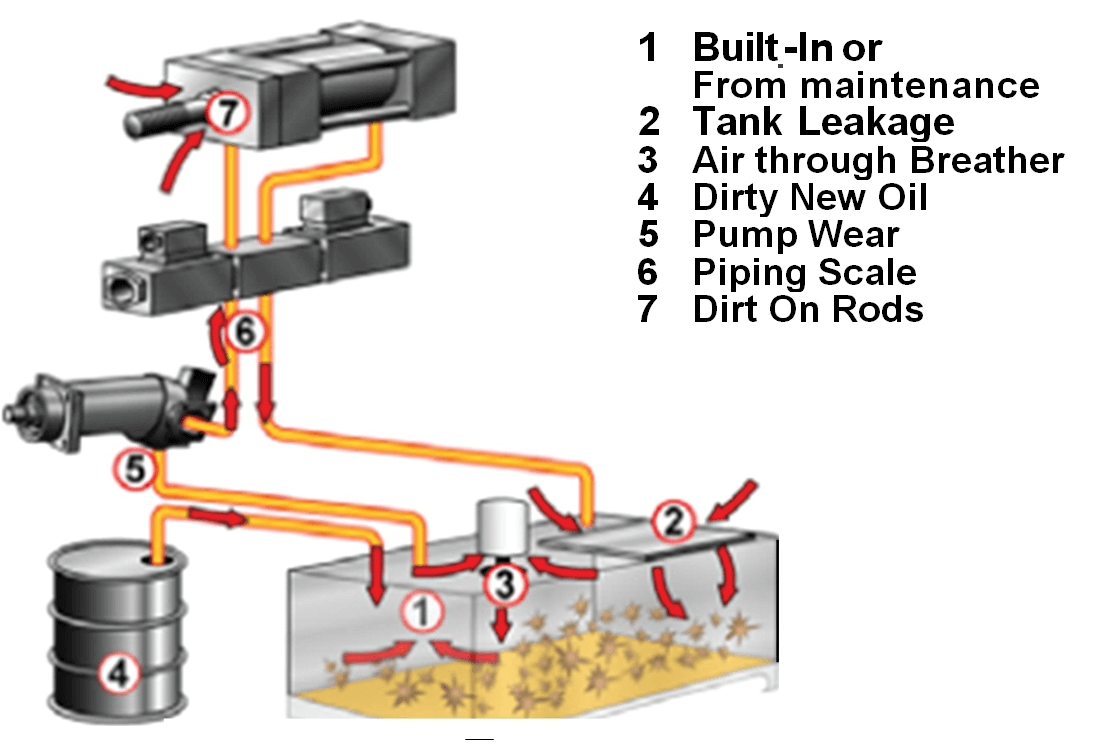
Sources of Contamination
The experience of designers and users of hydraulic and lube oil systems have verified that over 85% of all system failures are a direct result of contamination!
The Cost due to contamination is staggering, resulting from:
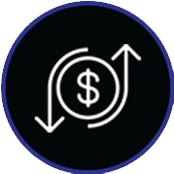
Loss of production (downtime)
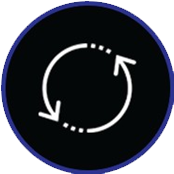
Component replacement costs
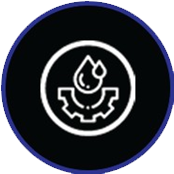
Frequent fluid replacement
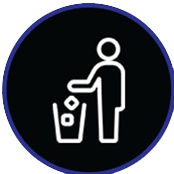
Costly disposal
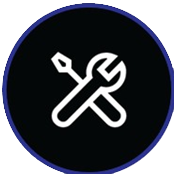
Increased overall maintenance costs
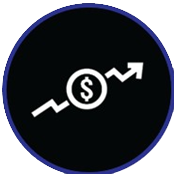
Increased scrap rate
Contaminant particles larger than 25 micron can jam pumps, valves and hydraulic motors. Smaller abrasive particles measuring between 0.5 and 5 micron known as silt which are about the same size as the operating clearances can cause wear, increase leakage, reducing, efficiency and increased temperature.
Contamination & Source
Particulate contamination is generally classified as ''silt'' or ''chip''. Silt can be defined as the accumulation of particles less than 5µm over time. This type of contamination also causes system component failure over time. Chips on the other hand, are particles 5µm+ and can cause immediate catastrophic failure. Both silt and chips can be further classified as:
Hard Particles
- Silica
- Carbon
- Metal
Soft Particles
- Rubber
- Fibres
- Micro organisms
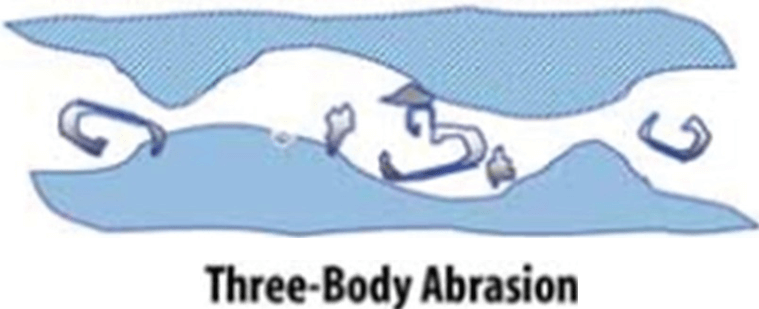
Contaminant Damage
- Orifice blockage
- Component wear
- Formation of rust or other oxidation
- Chemical compound formation
- Depletion of additives and oil degradation
Hydraulic fluid is expected to create a lubricating film to keep precision parts separated. Ideally the film is thick enough to completely fill the clearance between moving parts. This condition results in low wear rates. When the wear rate is kept low enough, a component is likely to reach its intended life expectancy, which may be millions of pressurisation cycles.
The actual thickness of a lubricating film depends on fluid viscosity, applied load, and the relative speed of the two surfaces. In many components, mechanical loads are to such an extreme that they squeeze the lubricant into a very thin film, less than l micrometre thick. If loads become high enough, the film will be punctured by the surface roughness of the two moving parts. The result contributes to harmful friction.
Table showing clearance in various pumps & control valves
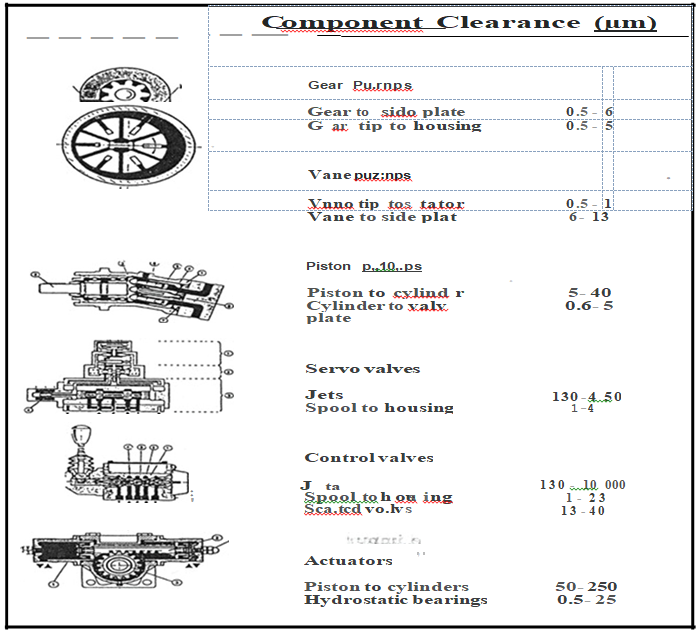
Why should we use super clean Hydraulic Oils?
In today's manufacturing world, reliable performance of equipment is very important and due to advancement in manufacturing process and design all the major equipment are being made with very close tolerances. Use of Super clean oils are must for achieving the reliable performance. It also provides the opportunity to achieve lower operating cost.
It is possible to differentiate normal hydraulic oil and super clean hydraulic oil based on NAS value provided by manufacturer of Hydraulic oil.
National Aerospace Standard has been developed to help measure the contamination levels of hydraulic fluids within hydraulic components.
National Aerospace Standard NAS 1638 Particle Counts Chart Contamination Control
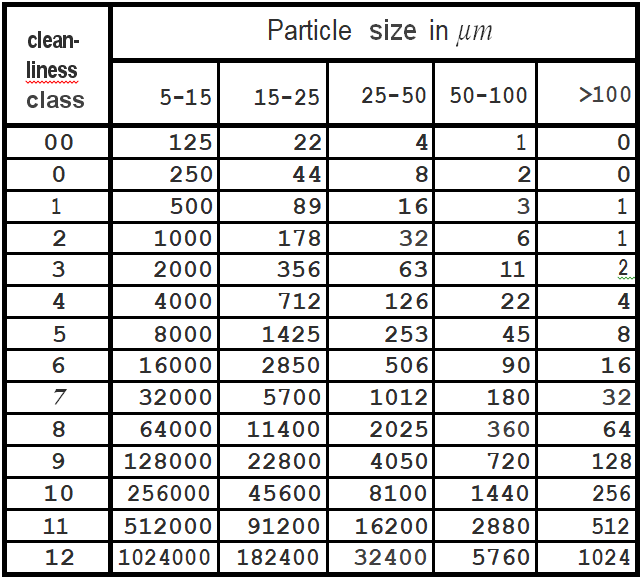
Lower the NAS value cleaner the Hydraulic oil
ISO 4406:99 is the reporting standard for fluid cleanliness.It is also referred to as ISO cleanliness code. This help in determining the cleanliness level of the fluid.
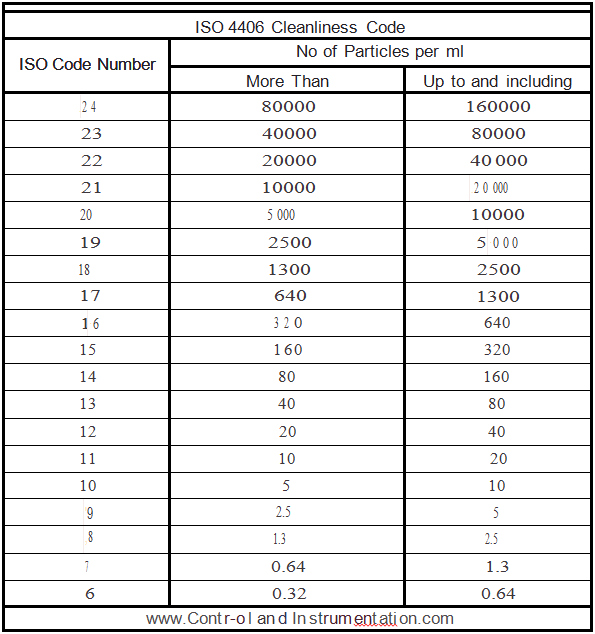
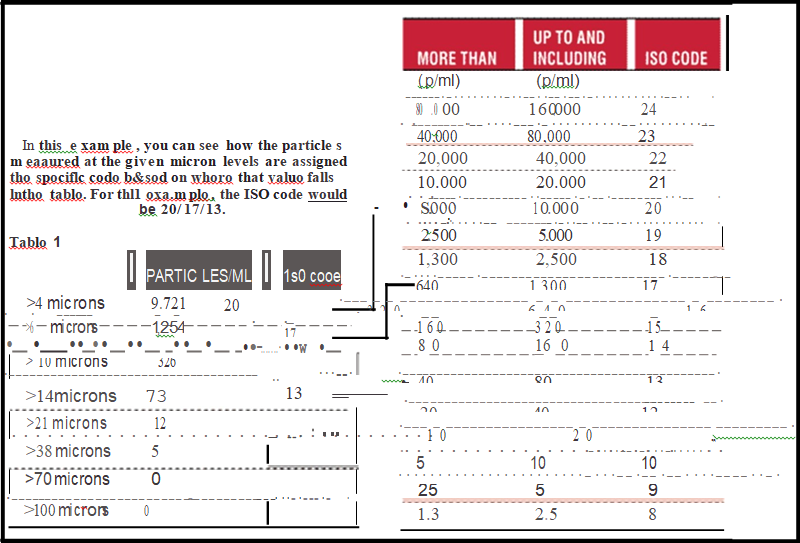
How can best performance be achieved with Super Clean Hydraulic Oil?
If used appropriately, super clean hydraulic oils ensures improvement in system performance and component life thereby reducing operating cost and improving system reliability.
In order to achieve best performance with super clean hydraulic oil it is important to follow best in house practices.
- Due care should be taken while filling oil from barrel to hydraulic tank. The hydraulic pump used to transfer oil from barrel to tank should be completely contaminants free.
- Use of offline filtration is a recommended practice in order to maintain continual desired cleanliness level. Offline filtration system can be portable electrostatic filtration machined or cartridge based filtration system.
- Breather at all instance should be closed properly to avoid contaminant entering the hydraulic tank.
- Online filter should be periodically checked and replaced.
- Sample should be analysed at regular intervals.
We at Hardcastle Petrofer have state of the art filtration system at our manufacturing plant at Sarigam which depending on the customer requirement can provide' hydraulic oils up to NAS 5 cleanliness level.
Our Range of Super Clean Fluids:
- Mineral based hydraulic oils Hilubric HLP HN Series
- Ester based hydraulic fluids Hilubric DU LLN Series
We offer free testing of oils to our customers at regular intervals to monitor the health of the fluids.