Cold Pilgering Process and Selection of Suitable Lubricant
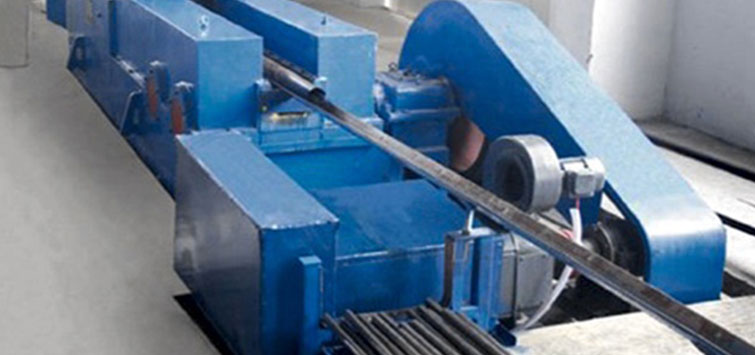
Introduction
Cold pilgering is one of the two major method used in seamless tube production. Other major method is cold drawing but cold pilgering has several advantages that are:-
- High production rate {upto6m/min for stainless steels)
- Decrease in eccentricity(30-50%improvement)
- Large area reduction{upto70-90%for different metals)
- Narrow dimensional tolerance {variations of less than10µm can be achieved)
- High surface quality {Ra values=50.4µm can be achieved) and
- Improving the grain structure of the material
This method is suitable for the most metals however different metals exhibit different maximum area reductions. This type of high precision tubes are demanded in a wide range of industries e.g, oil and gas, nuclear, medical, aerospace, heat exchanger,etc.
There are two common techniques of cold pilgering which are HPTR {High Precision Tube Roller) and VMR {Vertical Mass Ring). The main difference between these methods is that HPTR has constant cross-sections of groove and mandrel whereas VMR has much more complicated groove and mandrel design where the cross-sections vary along the rolling direction. This complex design enables higher output rates and makes VMR the most common technique. However, HPTR is preferred for some specific applications such as for tubes with extreme diameter to wall thickness {D/t) ratios, larger than100/1, for nuclear fuel cladding.
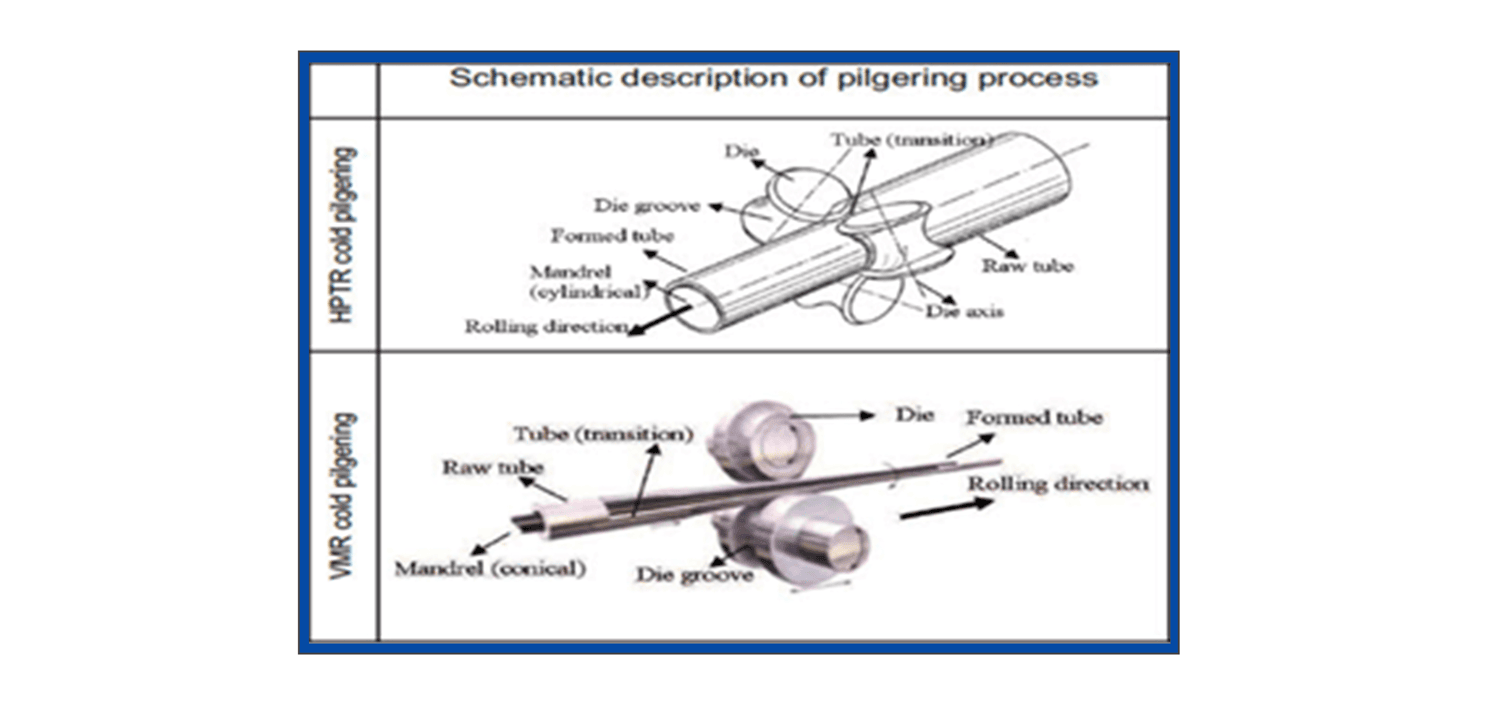
The basic idea of this method is to reduce both the diameter and the wall thickness of the tube and improving the grain structure of the material.The tube wall thickness is reduced and simultaneously it becomes elongated. The elongation contributes to the productivity of the method and is directly related to the amount of area reduction applied. This depends on the mandrel and roll die design and motions.
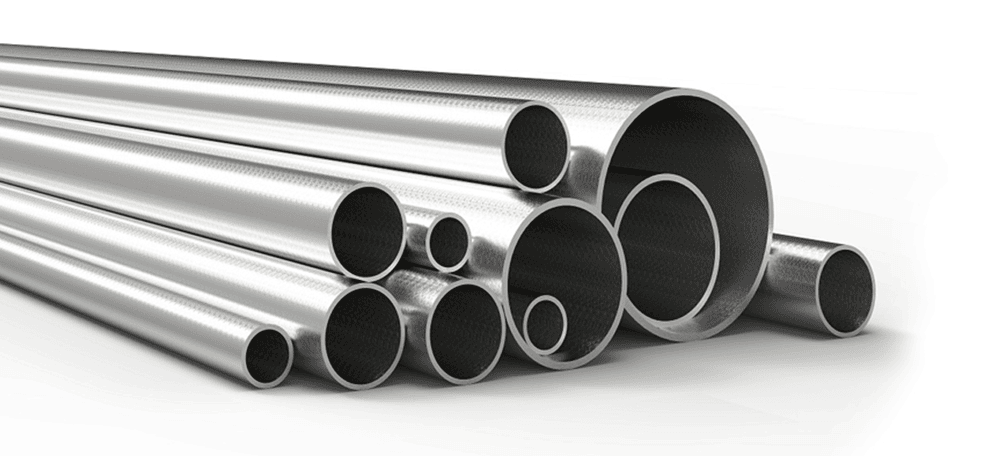
The preform obtained from a previous extrusion process, is subjected to repeated compression sequences between a stationary conical mandrel and two vertical roll dies. They are moving back and forth, called a stroke as indicated in Figure {below). The tube is fed a small amount, commonly 1-10mm, forward and rotated a certain degree when the rolls are at the inlet and/or outlet positions. They are not in contact with the groove at these locations by means of special design of dies. The use of many small feeding steps ensures a large area reduction without initiating cracks. The perform has a certain amount of eccentricity, which is not desired in high precision tubes. Furthermore, the tube is ovalised during the compressions in the cold pilgering process due to the side relief of grooves. The rotation steps are therefore applied so that the eccentricity and ovality are reduced until a virtually homogeneous wall thickness is obtained.
The mandrel is connected to a mandrel rod, shown in the Figure below, which is supported by a mandrel chuck {hydraulic clamp). This chuck is used to prevent the axial movement of the rod and also rotate it after strokes. The perform is supported by a feed chuck. Similarly this chuck is used to prevent the axial movement and also feed/rotate the perform after strokes. Roll dies are housed within a roll stand {also called a saddle) which is moved back and forth by a crank drive system. The finished tube is supported by an outlet chuck to prevent vibrations and bending due to the gravity. Moreover, the tube surface is continuously lubricated by oil jets to decrease the Tools {mandrel and roll dies)
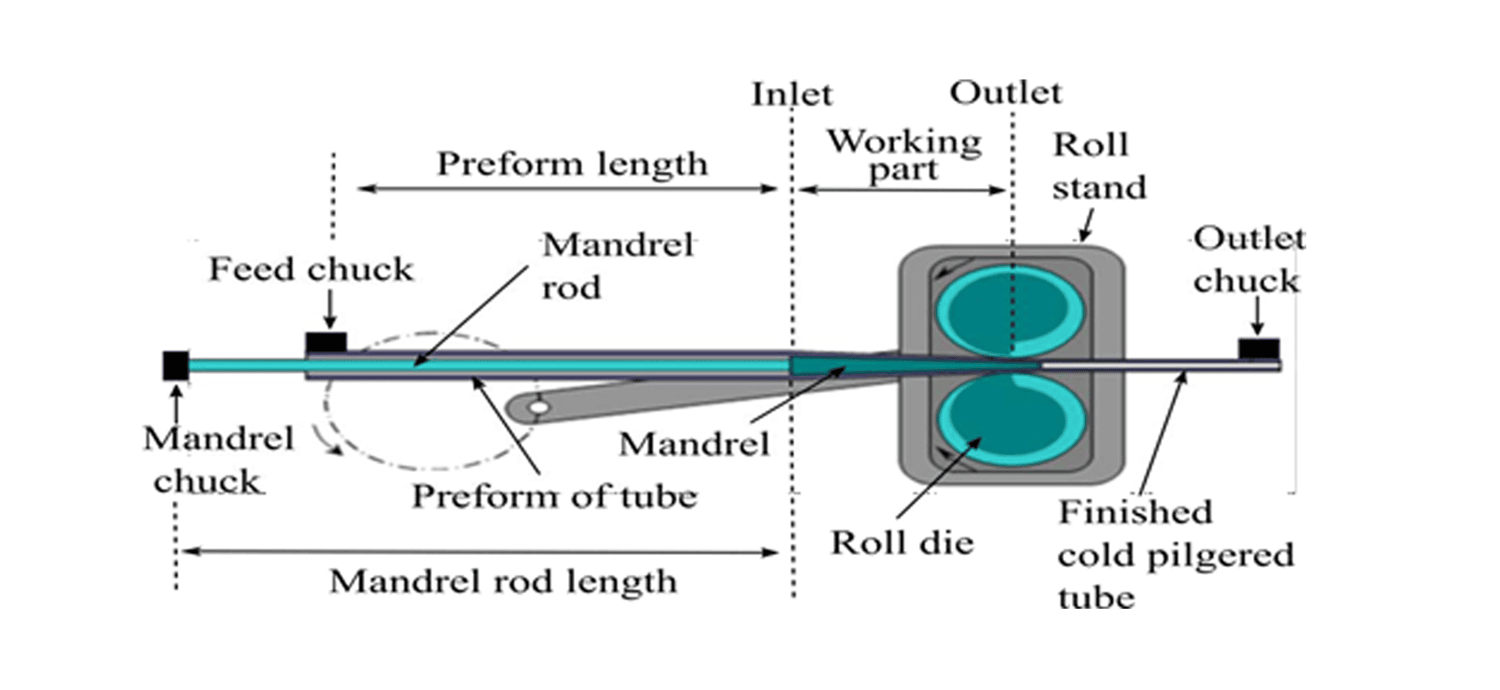
Tools
(Mandrel and roll dies)
Since the pilgering tools determine the shape of the pilgering cone and the final tube, they are the most important and complex elements of the cold pilgering operation. The tools consistent of a mandrel and two roll dies. They determine the inner diameter {ID) and outer diameter {OD) reductions of the preform, respectively. The forming operation is performed within two sections; the working section, where the OD/ID of the preform is progressively reduced and the sizing section where the ovalitity of the tube is decreased without area reduction temperature due to heat generated by the friction and large plastic deformation.
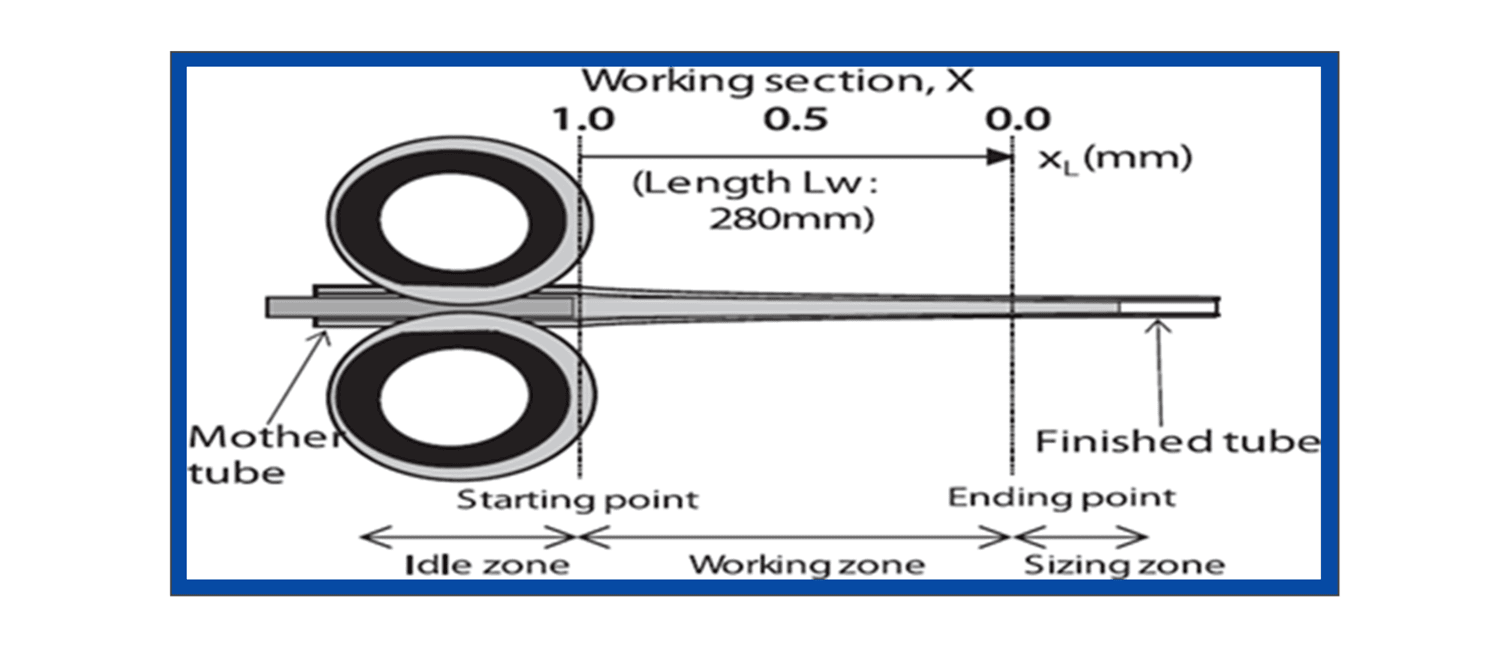
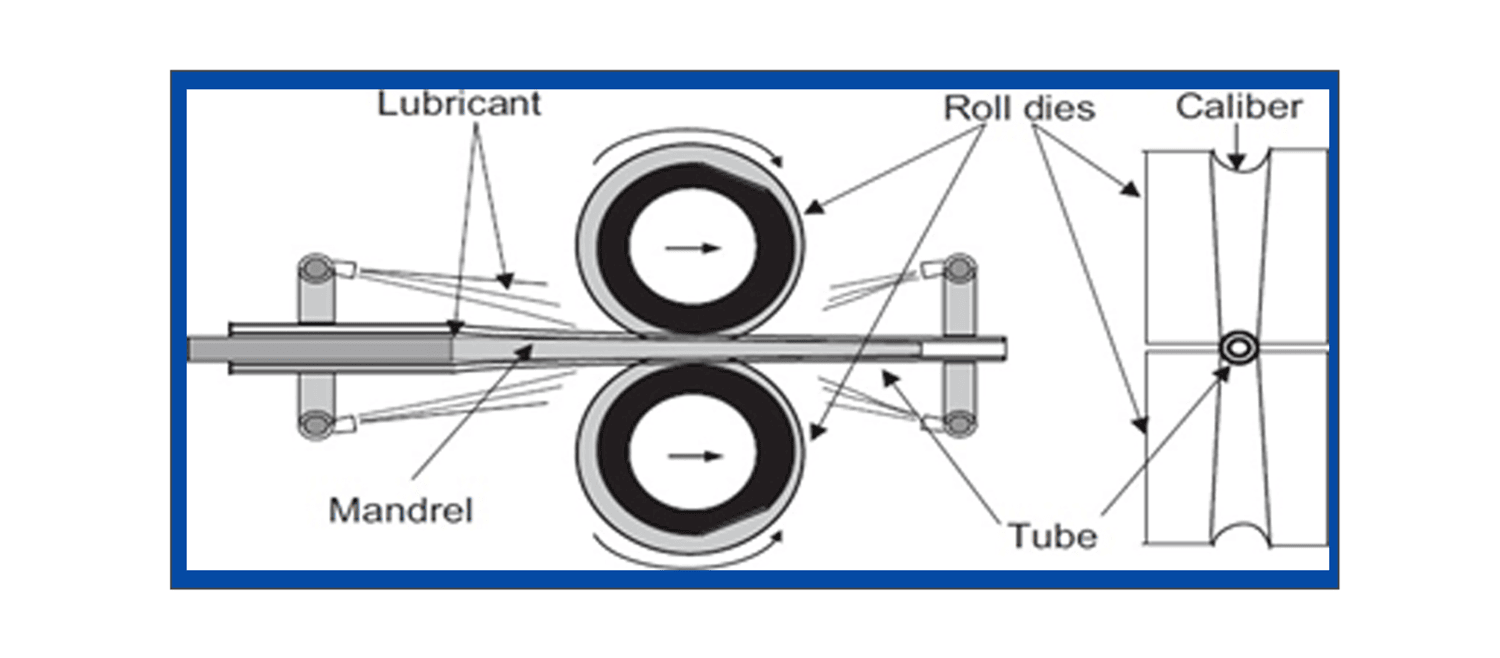
Lubrication
Lubrication is a key factor in the cold pilgering operation in terms of productivity as in most metal forming operations. This is due to several reasons.
First of all, it preserves the surfaces quality of the tool and tube which is a highly important criterion for cold finishing processes. A bad lubricant increases the friction and accelerates material transfer from the tube surface to the tool surface.Built up material on the tool surface causes scratches on the tube, making it necessary to grind the surface of the tool more often, and reduces tool Iife.
Secondly, it functions as a coolant to reduce the heat generated by friction between the work piece and the tool. Temperature control is important as a too high temperature may burn the lubricant.
Thirdly, it prevents the preform from getting stuck on the mandrel.
- Provides extreme pressure lubrication & cooling to the mandrel
- Prevent scratching of the mandrel
- Maintain high quality surface finish on the inside of the tube
- Lubricates the roller to reduce wear
- Lubricate the machine parts
LUBRICANTCHEMISTRY
As the tube drawing application being most sever application and the film formed at the contact points of tube surface and die is very thin, the additive selected such as highly chlorinated EP and Sulphur form are active stable film on the surface of contacts of both ID &OD of the tube as it is undergoing plastic deformation at high temperature and releases nascent chlorine and sulphur molecules on the films to protect it from further damage and maintains high quality surface finish both inside and outside of the drawn tube. It also protects mandrel and roll dies from wear and extend their life. Utmost care has been taken to select most ideal and high temperature stable chlorinated EP additives with suitable molecular chain to meet the environmental norms
Friction
- In general, the friction in metal forming operations is an important factor
- It dissipates energy, thus increase the needed force for desired deformation.
- A large fraction of the dissipated energy increases the temperature.
- Furthermore, it causes wear of the contacting surfaces.
- Moreover it afftects the material flow and homogeneity of deformation.
There are several factors influencing the friction such as
- The contact topology
- Material properties
- Relative sliding velocity
- The presence of lubrication
The contact condition in the cold pilgering process is mainly placed in the mixed lubrication region. In this mixed lubrication region, the friction is determined by the composition of influences from the asperities and the lubricant behavior.
The lubricant behavior is mainly influenced by the viscosity, contact pressure, relative siding speed and film thickness where as the concentration of the asperities of work piece and tools influences the real contact area.
Product Selection criteria
Will depend upon the following machine conditions
These verity of the operation condition
- Load
- Feed rate
- Stroke rate
- Type of material
- Input tube Dia and thickness etc
- Other consideration such as cleaning or machine lubrication
The following criteria are considered when selecting lubricant by customer
- Lubricity performance
- The environmental issues
- The corrosion protection
- The influence of lubricant and flow on friction and surface topology
Considering the above criteria HPPL has developed Neat oils with suitable viscosity which forms optimum film thickness to reduce the friction. This film thickness depends on the viscosity of the oil selected.
For further details about the recommendation/selection of products to suit to your machine & operation conditions you may please contact our Sales & Services department.
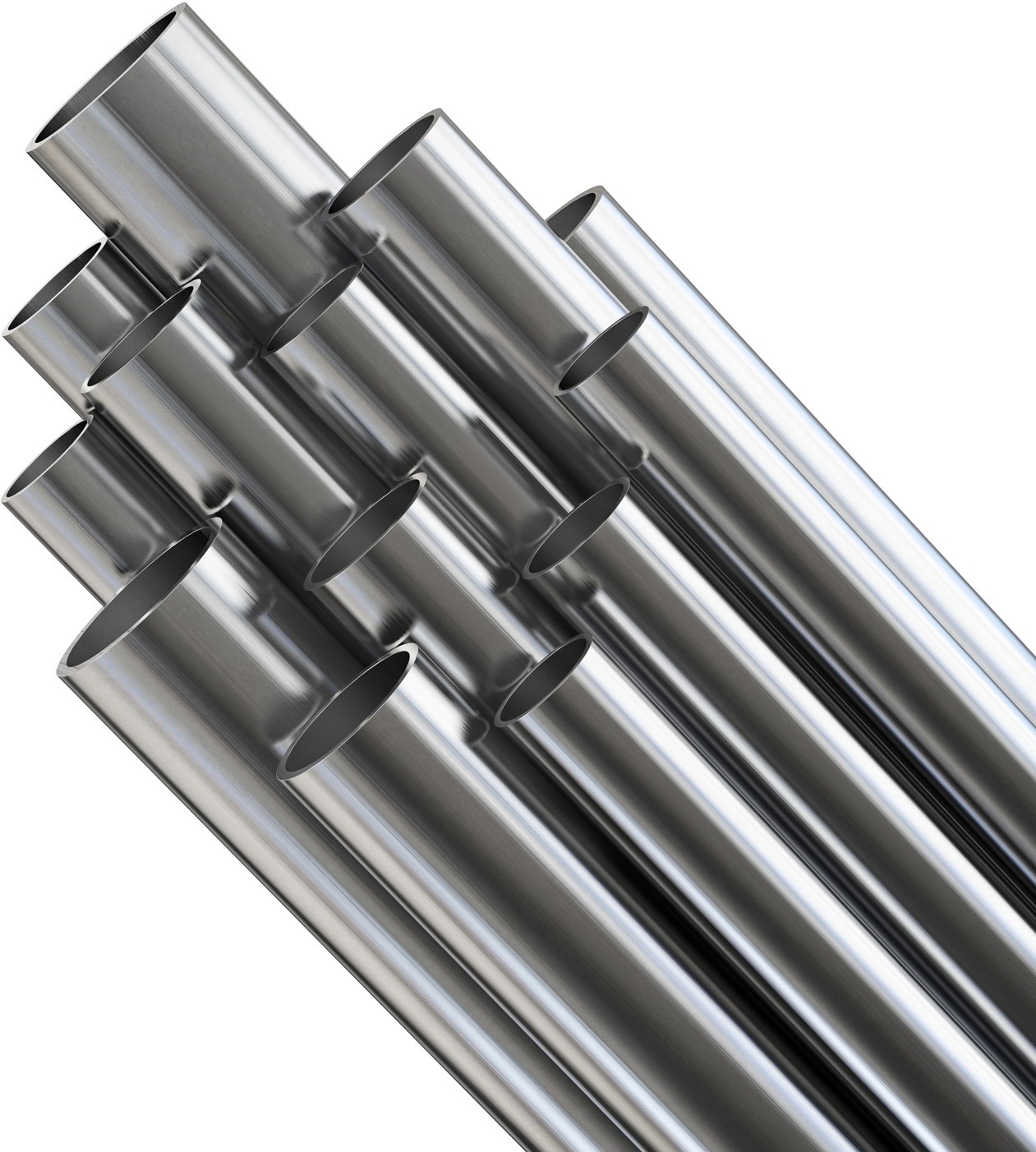