Rolling Process for Steel
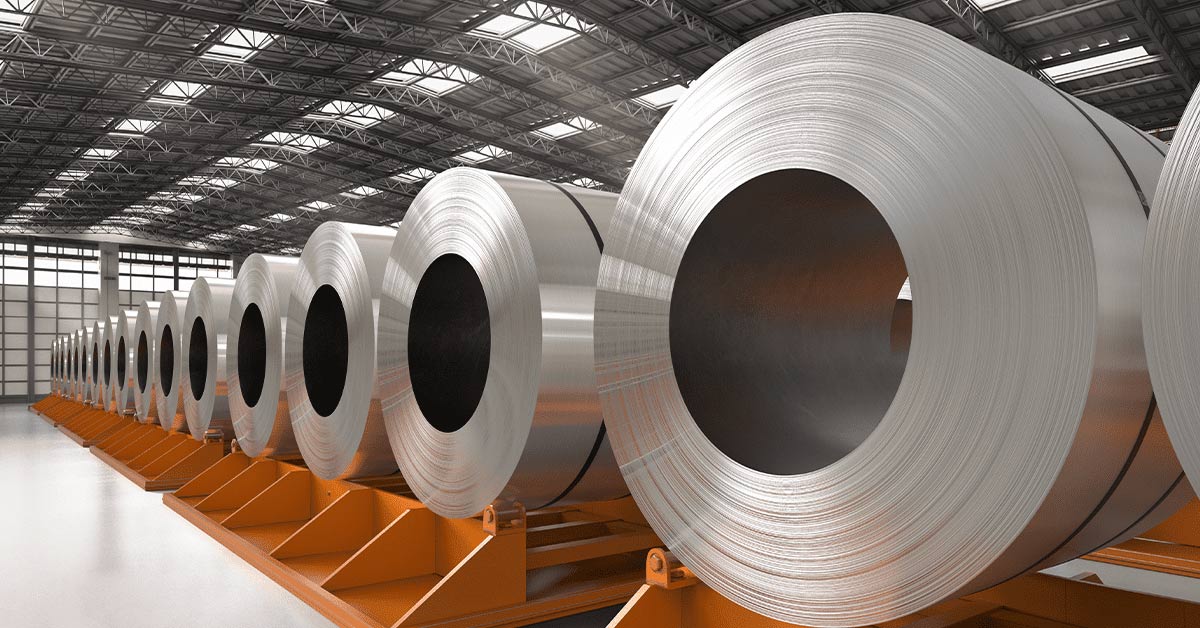
Steel undergoes the process of rolling to reduce the thickness of the metal as well as make it uniform. In this process, steel is placed between two/multiple rolls where the thickness is altered by manipulating the length direction of the steel rather than the width direction. This is because the point of contact between rolls along the length is much smaller than the width of the steel sheet that is pushed in between. This makes sure that the length of the steel is worked on and the working of the roll along the width is restrained.
Types of rolling
There are two types of rolling process: hot and cold rolling process. The basic distinction between these two processes is the difference in the processing temperature with regards to the recrystallization of the steel. When the processing temperature of the deformation of steel is above the recrystallization temperature, it hot rolling. On the other hand, if the processing temperature is below the recrystallization temperature, it is cold rolling.
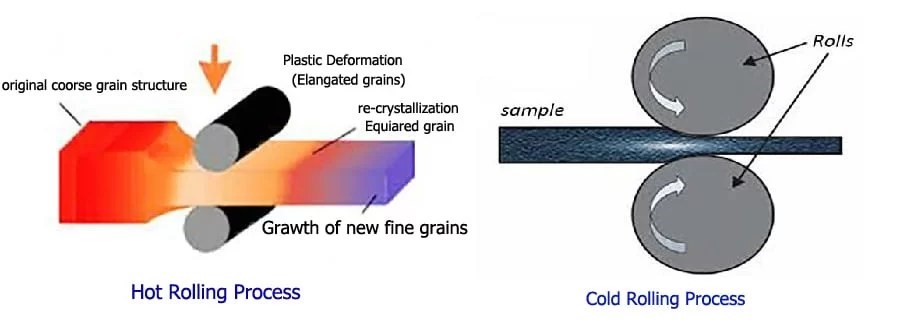
Hot rolling process
It makes the steel soft and ductile. The hardness of steel cannot be modified after the hot rolling process. The hardness is related to chemical composition of the metal as well as the rate of cooling. Hot rolling, however, may lead to loss of steel because of oxidation and result in poor surface finish.
Cold rolling process
In case of cold rolling, the hardness is much more than the hot rolling process. This process helps to obtain physical qualities of metal that are usually not obtainable by the hot rolling process. This can eliminate the errors like that of shrinkage. In short, cold rolling results in a final metal sheet that is more accurate in terms of dimensions and properties than the one that is obtained from hot rolling process. The metal sheet has a smoother surface and the strength of the steel is also increased. However, the ductility decreases. The strain makes the steel more brittle. Further, the final metal obtained needs to undergo heating regularly to make it workable.
The basic of rolling process of steel
Both horizontal and vertical stresses caused by the rolls compresses as well as restrain the steel. The rolls exert a vertical stress on the piece of steel and at the same time the price of metal exerts pressure back on the rolls. The rolls are exposed to elastic deformation because of the pressure induced by the piece of metal.
It leads to uneven distribution of thickness of the steel in such a way that the thickness is greater in the center and reduces as it moves along the edges of the metal. A thicker center indicates that the edges of the steel are more elongated. This implies that the edges are subjected to more stress and there is also more tension in the center of the working metal. The uneven thickness can lead to flawed final sheet of steel. It can cause warping, cracking or wrinkling of the steel sheet.
To counter this, back-up rolls are used. Otherwise, you can also use materials like sintered carbide that are high elastic modulus. Sometimes, cambered rolls are also used to counter elastic deflection of rolls. Depending upon the width of steel involved in the rolling and the stress flow, the degree of cambering can be decided. Insufficient cambering or absence of cambering can result in steel that has thicker center. On the other hand, if over cambering happens, it will make the edges thicker than center, which just the exact opposite of insufficient cambering. This can lead to splitting, wrinkling and cracking of edges of the final sheet of steel.
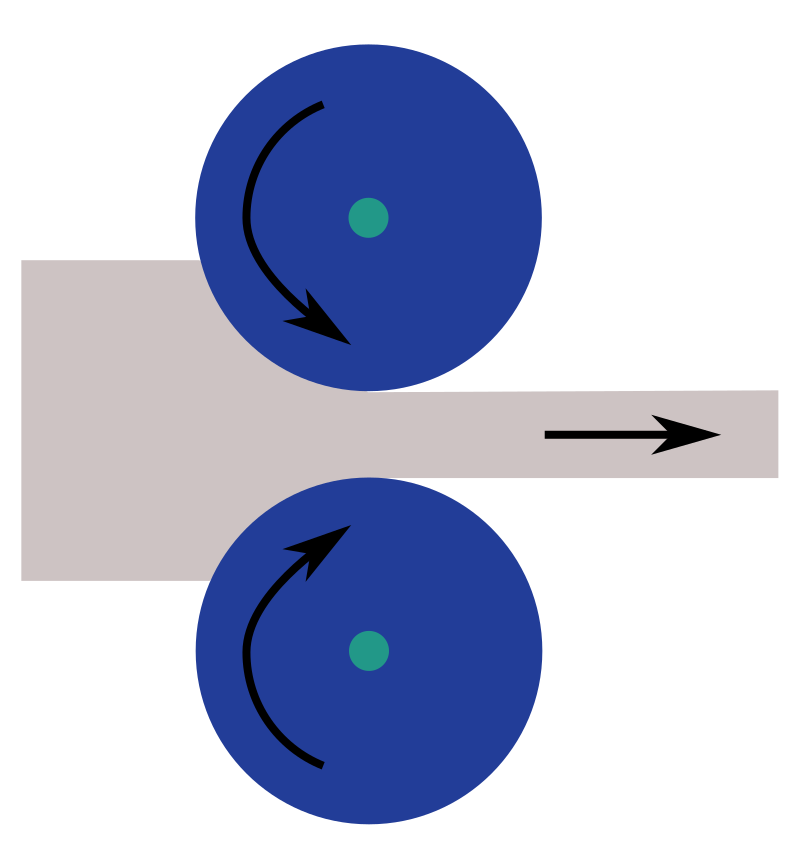
In the rolling process
- The arc of contact between the rolls and the metal is a part of a circle.
- The coefficient of friction, µ, is constant in theory, but in reality µ varies along the arc of contact.
- The metal is considered to deform plastically during rolling.
- The volume of metal is constant before and after rolling. In practical the volume might decrease a little bit due to close-up of pores.
- The velocity of the rolls is assumed to be constant.
- The metal only extends in the rolling direction and no extension in the width of the material.
- The cross section normal to the rolling direction is not distorted
Type of Cold Rolling Mills :
- Two High
- Four High
- Reversible
- Tandem
- Six High
- Reversible
- Tandem
- Cluster
Cold Rolling Oils
During cold rolling of steel, liquid coolants are used to control heat generation at the roll bite. This coolant can also be used for roll bite lubrication in Hot Rolling Mills. Roll lubrication technology can be used to reduce the rolling loads in the mill and entails adding oils to the water coolant to form an oil in water emulsion of varying emulsion stability to suit requirements of different rolling parameters of mills, which reduces the friction between the strip and work rolls. Sheet and tinplate cold rolling mills worldwide are continuously looking for ways to increase productivity, improve product quality and overall costs of production.
Types of Rolling Oil
Based on emulsion stability it can be divided into a) stable emulsion forming, b) meta stable emulsion forming and c) unstable emulsion forming. It can be noted that stability of emulsion is not only the choice of rolling oil formulation for any mill’s application but it also requires the nature of emulsifiers. There are four types of emulsifiers a) Cationic b) Anionic c) Non-ionic and d) Amphoteric. Generally, Non-ionic and Cationic type emulsifiers are in use in rolling oil formulation.
RAW MATERIALS
Evolution of cold rolling oil is passing through mineral oil based formulation to the present state of art technology based on synthetic esters with controlled droplet sizes where emulsifiers is of cationic, amphoteric or nonionic in nature. Like other evolution . this also is for meeting the time dependant requirement of end users cold rolled steel.
Five major considerations in selecting a lubricant/oil for cold rolling has been depicted elsewhere under lubrication in cold rolling. Therefore, selection of raw materials for a good cold rolling oil for steel is of paramount important. There are five different groups of chemicals in a cold rolling oil formulation like, base fluid , emulsifiers, extreme pressure & anti-wear additives, anti-rusting additives and biocide as an optional . Generally, base fluids are selected from mineral oils, natural esters like tallow, vegetable oils and synthetic esters.
Rolling oil formulations based on natural fats have certain limitations like more scum formation due to its inherent nature of broad distribution of oil in water emulsion . Less shear stable hence inconsistent performance with time. More prone to biodegradation leads to comparatively lower emulsion life resulting in more oil consumption. On the other hand, products based on synthetic esters have the following benefits:
- Less scum generation due to its easy disperse ability in water with more defined droplet sizes of oil in water leads to less oil consumption.
- More shear stable resulting in consistent performance of oil with time.
- Less prone to bio-degradation ensures more emulsion life and less oil consumption.
It is widely accepted that cold rolling involves mixed lubrication, a mix of hydrodynamic and boundary lubrication.
Selection of Rolling Oil :
To select a rolling oil for a mill generally following points are considered :
- Mill configuration
- HR sheet composition
- Mill speed
- Input/output thickness
- Sheet width
- Maximum load of mill
- Mill control system
- Coolant Flow rate
- Coolant wiping system
- Downstream processes
- Coolant system
- Water quality for coolant maintenance
- Instances of tramp oil contamination
To meet the different mill requirements, in general rolling oil formulations are divided into three categories based on saponification value.
Width, mm, max | Mill speed Mpm, max | Output thickness, mm, min | % reduction,max | Saponification Value | ESI |
---|---|---|---|---|---|
500 | 500 | 0.12 | 90 | 100 to 130 | 0.87 to 0.90 |
1000 | 500 | 0.20 | 90 | 140 to 180 | 0.70 to 0.80 |
1000 | 1000 | 0.12 | 90 | 180 to 190 | 0.60 to 0.70 |
> 1000 | 1400 | 0.12 | 90 | 190 to 210 | 0.55 to 0.65 |
> 1000 | > 1400 | 0.12 | 90 | 190 to 210 | 0.3 to 0.50 |
Hiroll NW & Hiroll BW series of cold rolling oils and Hiroll HR series of hot rolling oils are customized to meet the different mill requirements.